Aluminum Composite Panel(ACPs) Coatings: Pick the Right Paint
Aluminum Composite Panel(ACPs) Coatings: Pick the Right Paint
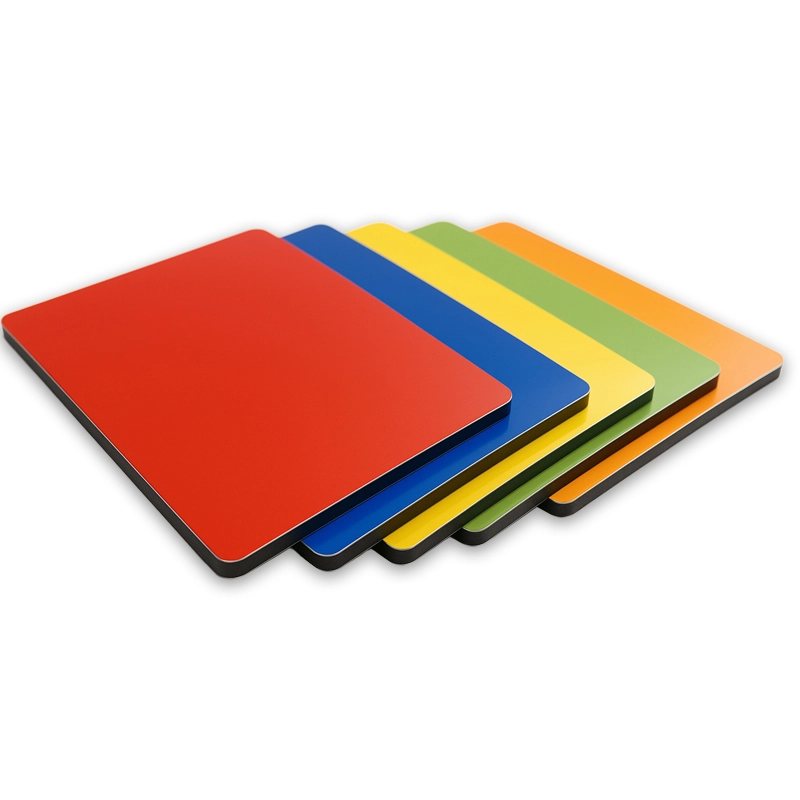
acm sheet
Aluminum composite panels (ACPs) are used everywhere. Buildings, signs, and more use them. They look smooth and modern.
The outside of an ACP has a special layer. It’s like paint. This layer is called a coating. It keeps the aluminum safe. It also gives the ACP its color and shine.
Choosing the right coating matters. It changes how the ACP looks. It also decides how long it will last. Some coatings work better in some places than others.
Let’s learn about different ACP coatings. We will see where each one works best.
Polyester (PE) Coating: Good for Indoors
Polyester (PE) coating is a common choice. It’s a basic type of paint. It is often used for things inside buildings.
What is it? PE coating is made from polyester. Polyester is a type of plastic. The paint goes on in layers. Then, it gets baked to become hard.
Why choose PE?
It’s cheap: PE coating usually costs less than others. This is good if you don’t have a lot of money.
It can bend: ACPs with PE coating can be bent a little. The paint won’t crack easily. This is useful for making curved shapes.
Lots of colors: PE coating comes in many colors. You can find the exact color you want.
Smooth look: PE coating makes the surface smooth. This is great for printing words and pictures on signs.
What are the downsides of PE?
Not very strong: PE coating can get damaged by the sun. The color might fade over time.
Weak against chemicals: Some strong cleaners or chemicals can hurt PE coating.
Not the best for outside: PE can be used outside. But it might not last as long as other coatings.
Where should you use PE coating?
Inside walls: PE is good for walls inside buildings. It looks nice and doesn’t cost much.
Indoor signs: The smooth surface is perfect for signs inside stores or offices.
Short-term outdoor signs: If a sign is only going to be outside for a little while.
Places without much pollution: PE might get damaged in very dirty or smoky areas.
Think of it like: The paint on your bedroom walls. It looks good inside but might not handle the outside weather very well.
Polyvinylidene Fluoride (PVDF) Coating: Tough for Outdoors
Polyvinylidene Fluoride (PVDF) coating is very strong. It can handle tough weather and lasts a long time. It is often used for the outside walls of big buildings.
What is it? PVDF coating is made from a special plastic called fluoropolymer. It has very strong parts that make it stable. Usually, it has a few layers. There’s a layer to help it stick, a layer with the color, and a clear layer on top.
Why choose PVDF?
Handles all weather: PVDF can stand strong sunlight, rain, and very hot or cold temperatures. It won’t fade or get chalky easily.
Resists chemicals: Most chemicals won’t hurt PVDF. This is great for cities and places with factories.
Lasts a long time: Buildings with PVDF coated ACPs can look good for many, many years. You don’t need to fix them often.
Keeps its color: The colors of PVDF coatings stay bright for a long time.
What are the downsides of PVDF?
Costs more: PVDF coating is more expensive than PE. The strong materials make it cost more.
Doesn’t bend easily: ACPs with PVDF coating are not as easy to bend into shapes.
Fewer color choices than PE: You can still get many colors, but maybe not as many as with PE.
Needs special workers: Putting on PVDF coating needs special tools and skills.
Where should you use PVDF coating?
Outside walls of buildings: Tall buildings, shopping centers, and airports need coatings that last.
Curtain walls: These are the outside walls that don’t hold up the building. PVDF’s strength is important here.
Buildings in polluted areas: The coating won’t get damaged by smoke and dirt.
Buildings that need to look good for many years: PVDF makes sure the building looks new for a long time.
Think of it like: A super strong, expensive raincoat for a building. It protects against everything and lasts for years.
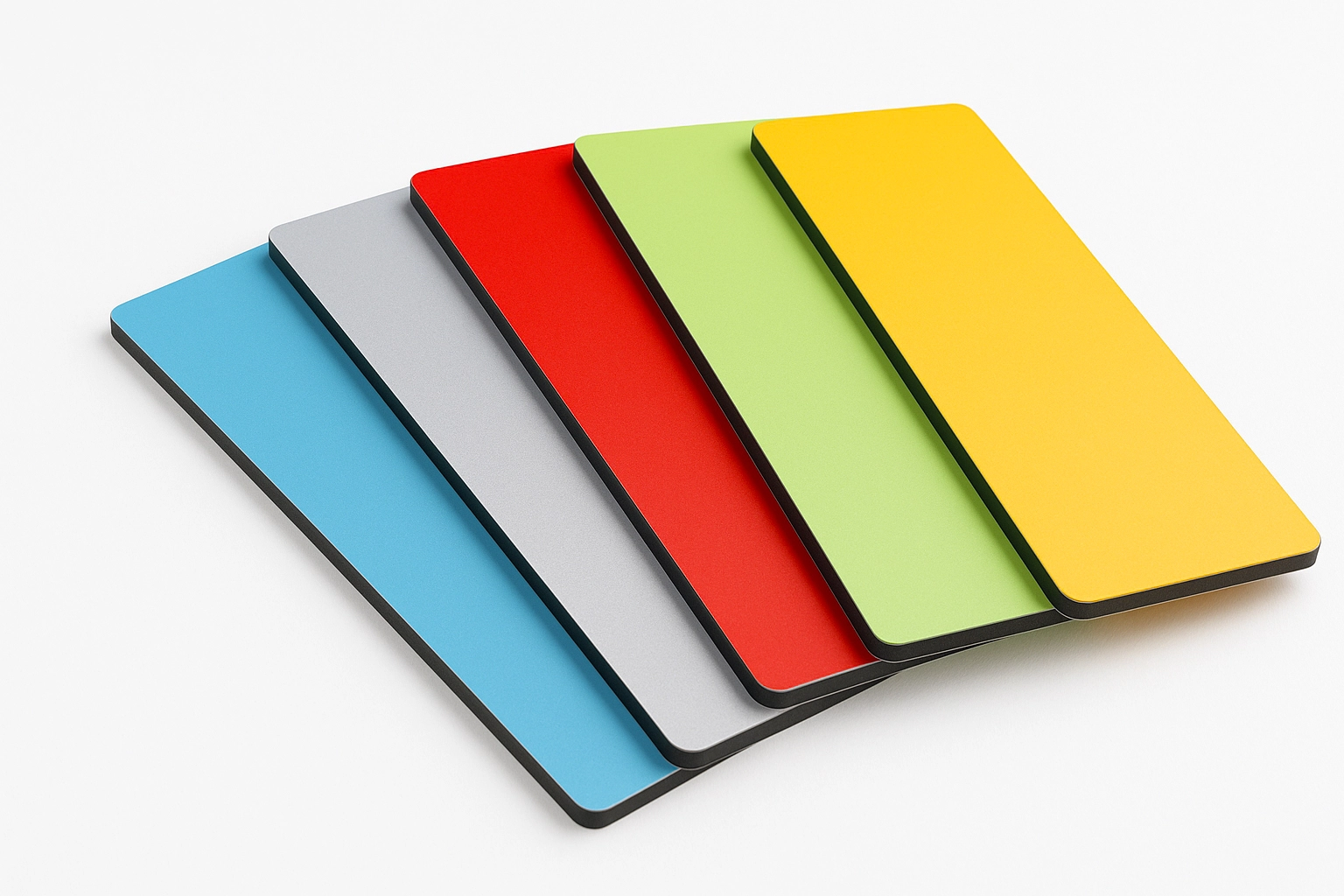
Aluminum Composite Panels
Anodized Finish: A Metal Look
Anodizing is different from painting. It’s a way to change the metal itself. It makes the aluminum stronger and gives it a unique metallic look.
What is it? To anodize, you put the ACP in a special liquid and send electricity through it. This makes a hard layer on the aluminum surface. This layer is strong and won’t rust easily. You can also add color to this layer.
Why choose Anodizing?
Very strong and hard: The anodized layer is part of the metal. It’s hard to scratch or wear down.
Good against rust: The layer protects the aluminum from rusting.
Special metal look: Anodizing gives a unique metallic shine that paint can’t copy.
Lasts for decades: Anodized aluminum can look good for a very long time.
Can be eco-friendly: It can be better for the environment than some painting methods.
What are the downsides of Anodizing?
Limited colors: You mostly get metallic colors. Bright colors are hard to achieve.
Can get a white powder sometimes: In very harsh weather, a white powder might appear on the surface.
Hard to fix: If it gets damaged, it’s hard to fix it perfectly.
Not as bendy as paint: Anodized ACPs might crack if bent too sharply.
Where should you use Anodizing?
Metal parts of buildings: Window frames, door frames, and decorations that need a metal look and strength.
Places with lots of people: Surfaces that might get touched a lot, like entrances.
Projects that want a natural metal look: Anodizing shows off the beauty of the aluminum.
Near the ocean (special types): Some types of anodizing can handle salty air.
Think of it like: Making the metal stronger and changing its look, instead of just putting paint on top.
Choosing the Right Coating: Think About…
When you need to pick a coating for ACPs, think about these things:
Where will it be used? Inside or outside? Outside needs stronger coatings like PVDF .
How much money do you have? PE is cheapest. PVDF is most expensive. Anodizing costs can vary.
What look do you want? Do you need a specific color or shine? PE has many colors. Anodizing looks metallic. PVDF keeps its color for a long time.
What’s the weather like? Is it very sunny? Rainy? Polluted? PVDF is best for tough weather. PE is not ideal.
How long should it last? PVDF are made to last for many years. PE might need to be replaced sooner, especially outside. Anodized finishes also last a long time.
How easy is it to clean? PVDF is easy to clean. Other coatings might need more cleaning. Anodized surfaces are also usually easy to clean.
Is the environment important?
In Short
Picking the right coating for your ACPs is important. It affects how they look and how long they last.
Use Polyester (PE) for cheap, indoor projects.
Use Polyvinylidene Fluoride (PVDF) for tough, outdoor jobs in bad weather.
Use Anodized Finish for a strong metal look.
Think about where you will use the ACPs, how much money you have, and what look you want. This will help you choose the best coating.
Always talk to the people who make ACPs and coatings. They can give you advice for your specific project. They know about how their products work and how to install and take care of them. This will help your project look great and last for years.